
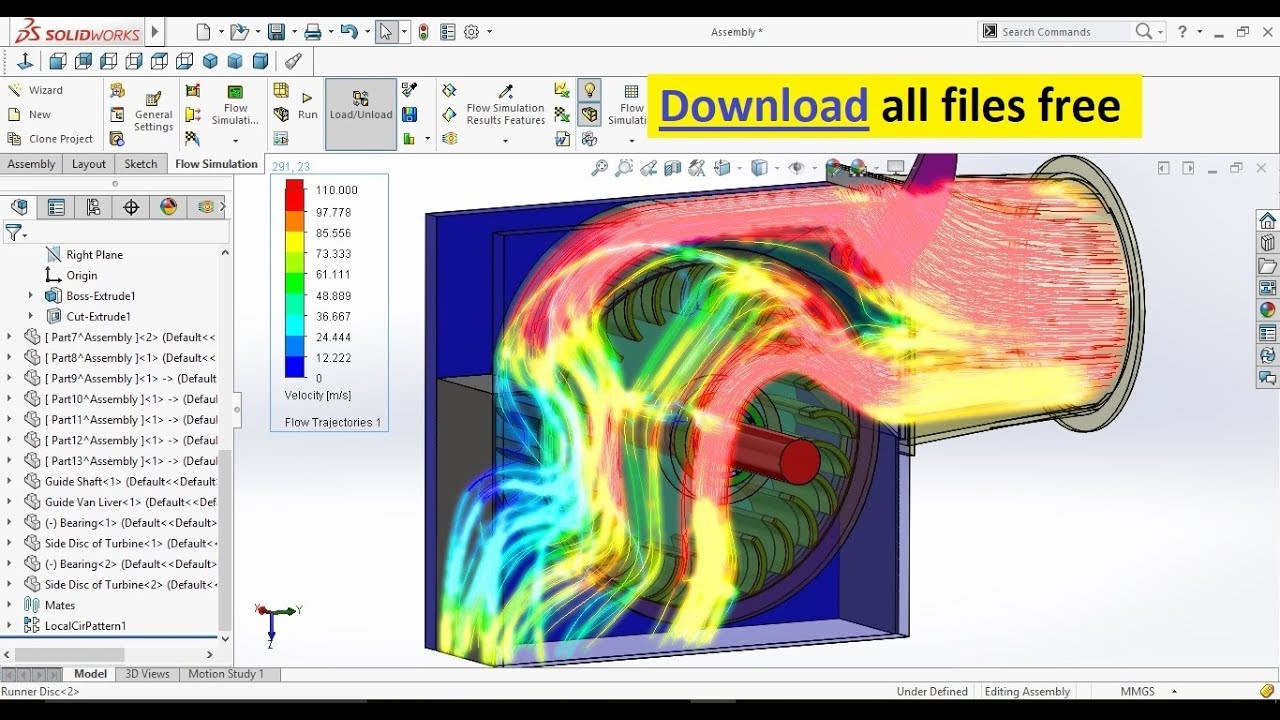
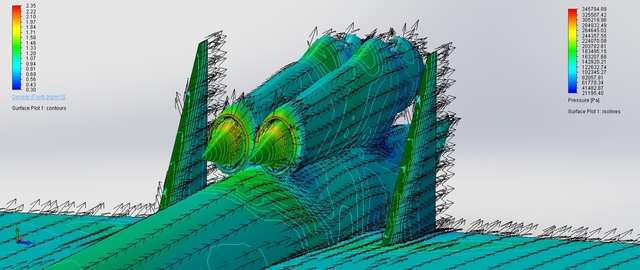
Wall with specified Heat transfer coefficient.Wall with specified Heat flux or Heat transfer rate.The following heat boundary conditions can be specified at the model walls in contact with fluid:.Symmetry boundary conditions, as well as ideal wall can be specified if necessary.Fans at models' inlets and outlets, as well as inside the computational domain can be specified.Ambient fluid conditions are specified at far-field boundaries in case of external analysis.Velocity, mass flow rate, volume flow rate, or pressure (static and total) boundary conditions are specified at models' inlets and outlets.In case of an external analysis, the computational domain covers the model's surrounding space.If heat transfer in walls is considered, the model walls are also included. In case of an internal problem, the computational domain envelopes the fluid volume inside a model.Computational domain’s boundary planes are orthogonal to the Cartesian coordinate system’s axes. Computational domain is a rectangular prism where the calculation is performed.This method is among preferred methods for fluid phenomena modeling. FVM is a general approach for both simple and complex problems.SolidWorks Flow Simulation solves time-dependent Navier-Stokes equations with the Finite Volume Method (FVM) on a rectangular (parallelepiped) computational mesh.They make many assumptions and fail to solve most practical problems. Analytical solutions are only available for simple problems.Analysis can help you optimize your designs by quickly simulating many concepts and scenarios before making a final decision.SolidWorks Flow Simulation analysis shortens the object's way to the market.

#SOLIDWORKS FLOW SIMULATION FREE DOWNLOAD SOFTWARE#
SolidWorks Flow Simulation is a fluid flow and heat transfer analysis software fully integrated in SolidWorks.SOLIDWORKS Flow Simulation software takes the complexity out of flow analysis and enables engineers to easily simulate fluid flow, heat transfer and fluid forces so engineers can investigate the impact of a liquid or gas flow on product performance.SolidWorks Flow Simulation Instructor Guide SOLIDWORKS Flow Simulation enables true concurrent CFD, without the need for advanced CFD expertise. Product engineers and CFD experts alike, armed with the power of SOLIDWORKS Flow Simulation, can predict flow fields, mixing processes and heat transfer and directly determine pressure drop, comfort parameters, fluid forces and fluid structure interaction during design. Flow Simulation allow you to simulate liquid and gas flow in real world conditions, run “what if” scenarios and quickly analyse the effects of fluid flow, heat transfer and related forces on immersed or surrounding components. Design variations can be compared to make better decisions, resulting in products with superior performance. Additional valuable modules, HVAC and electronic cooling, offer dedicated fluid flow simulation tools so you can go to the next level for your analysis.īuilt to tackle CFD engineering challenges, SOLIDWORKS Flow Simulation enables engineers to take advantage of CAD integration, advanced geometry meshing capabilities, powerful solution convergence and automatic flow regime determination without sacrificing ease of use or accuracy.
